Find information specific to your situation here.
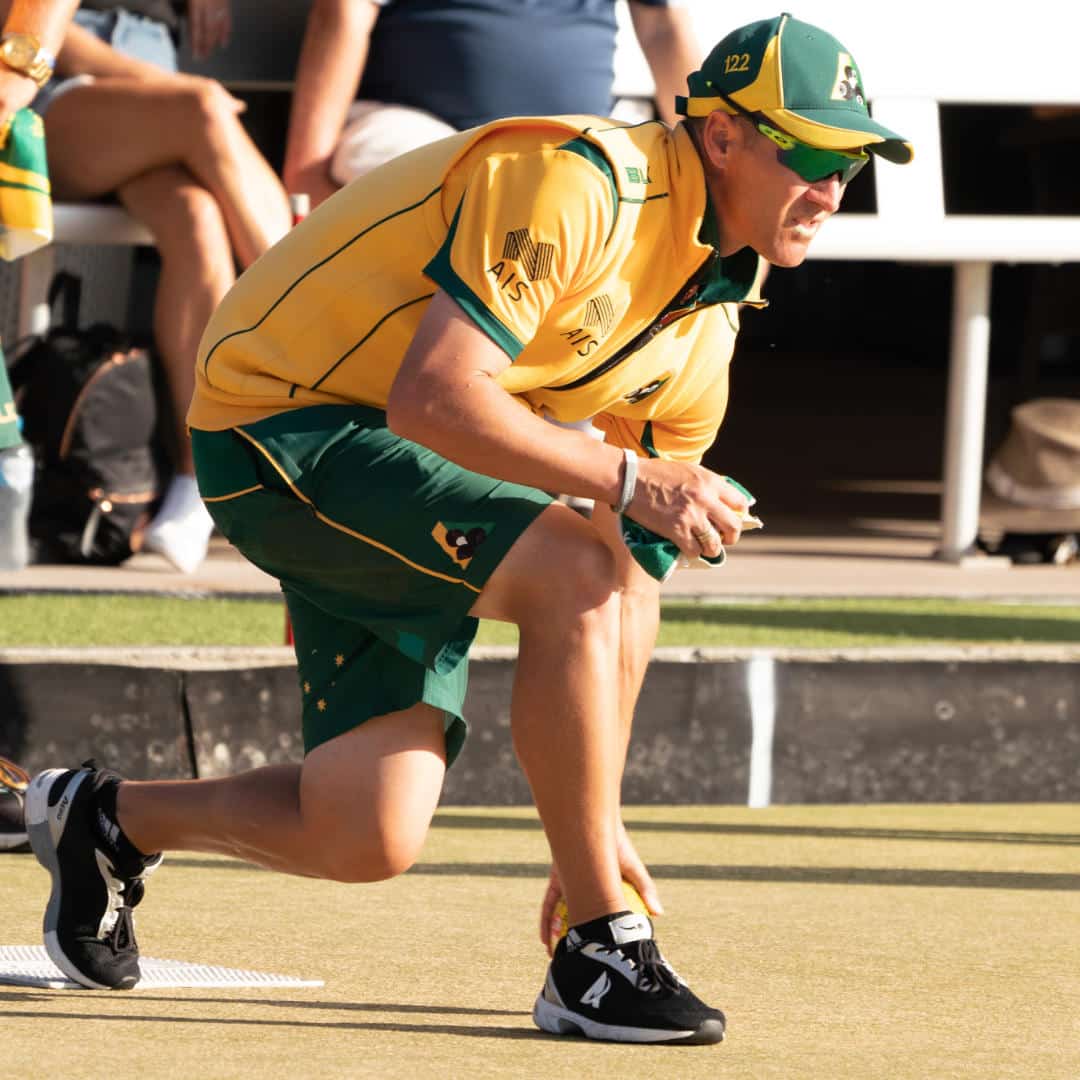
I'm from a club and want to explore LED lighting
Are you looking to move to the benefits of digital lighting? Have you assessed whether digital lighting will do what you want or expect?
Learn more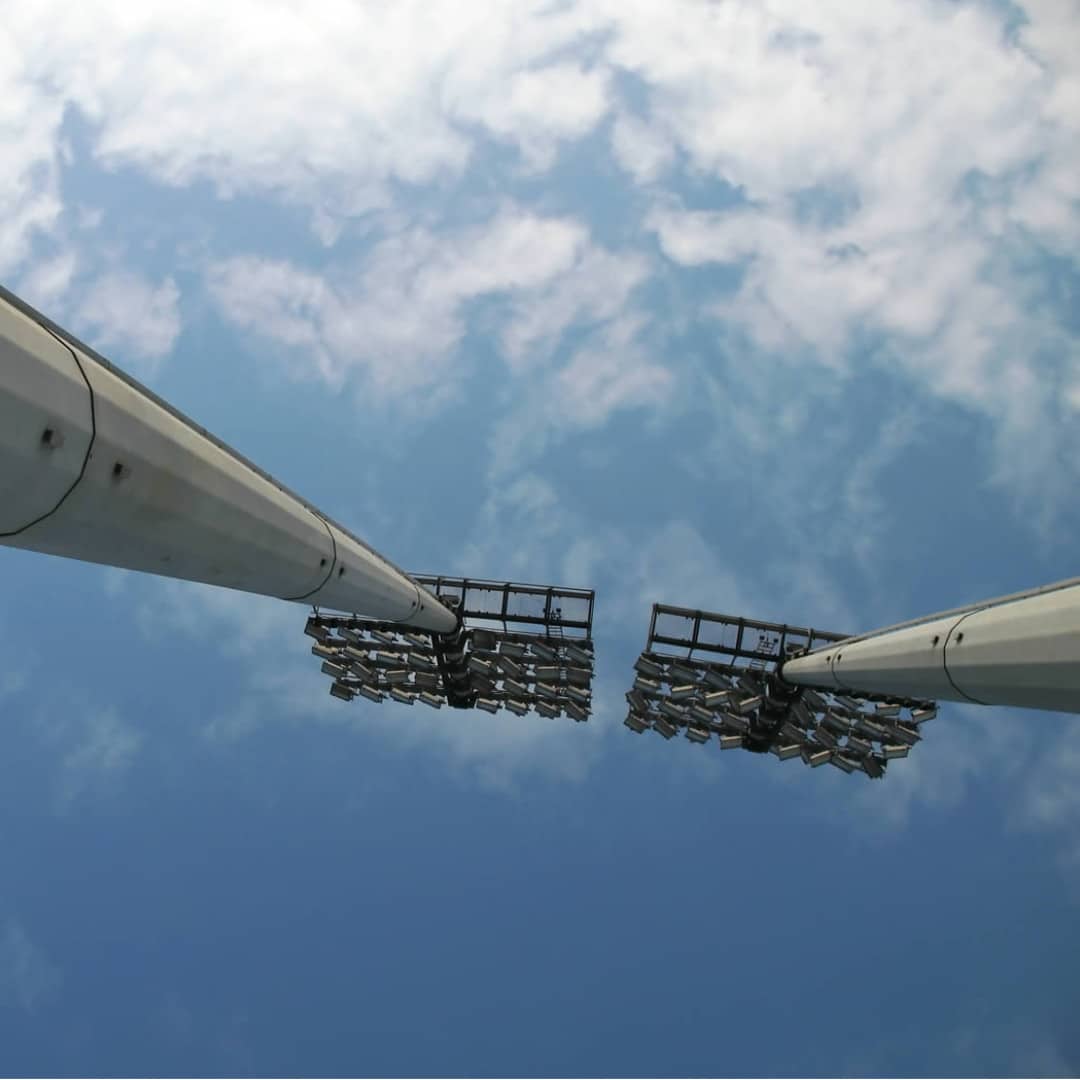
I'm a lighting architect looking for information
As a lighting professional you are already aware of the benefits of solid state lighting. Legacy can provide you with a refreshing LED Lighting alternative for your next project.
Learn more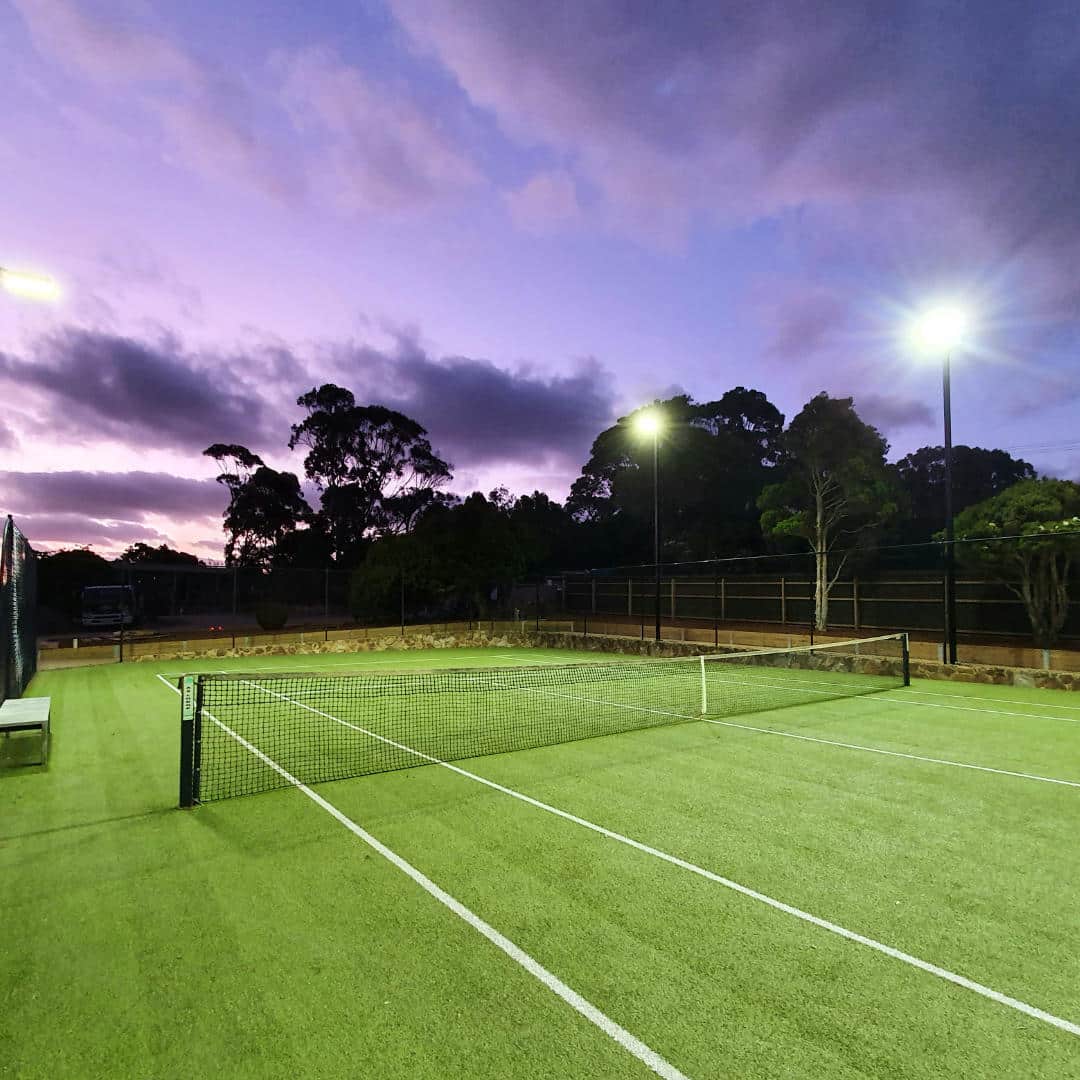
Submit your layout to receive a free lighting design
If you already know the required lux level for your facility, send your layout to us and we will create a free custom lighting design!
Submit plans